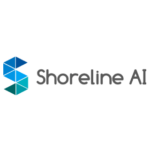
Shoreline’s plug-and-play asset performance management delivers breakthrough simplicity and cost efficiencies. Completely self-installed by non-experts, smart sensors automatically connect to the cloud and are auto-provisioned via a rich library of 30,000+ pre-built asset physics models.
Shoreline Chief Scientists, Internationally recognised for Reliability Engineering, Process Optimization and Corporate Transformation
The general belief of predictive maintenance is that it is a maintenance tool that uses vibration, infrared or lubricating oils analysis data to prevent catastrophic failure of, and unplanned production downtime caused by equipment failures. Because of this belief, predictive programs are set up with the singular mission of breakdown prevention without any focus, or even thought about, on the overall impact on these programs. While many of these programs have resulted in verifiable and measurable reductions in unscheduled downtime caused by asset breakdowns, they have increased overall maintenance cost and a decrease in overall plant performance.
Several factors have contributed to the negative results of traditional predictive maintenance programs. The fundamental reason that most programs have failed to achieve a marked improvement in overall plant performance is the breakdown mentality that continues to dominate the management philosophy of some corporations. Because of this attitude, we have failed to perceive the real benefits that a predictive maintenance program can supply and have not recognized the negative impact that this limited application has generated. These plants do not understand that high breakdown rates, as well as maintenance costs are the visible symptom of a much more serious design, buying, production or management problem which cannot be resolved by simply preventing catastrophic failure of critical machinery.
Another factor that has limited traditional programs is the improper use of diagnostic and analysis techniques. In most cases, existing programs have not used the real power that vibration, thermography, tribology and the multitude of other plant evaluation techniques can provide. To an extent, this limitation is the result of management philosophy that has evolved in our society. We tend to seek simple answers to the extremely complex problems that limit our ability to compete in the world market. As a result, too many plants do not use the full capabilities of the various predictive maintenance technologies.
The following guidelines will give you an overall evaluation of your program’s effectiveness:
The first step required deciding the effectiveness of your predictive maintenance program is to evaluate the change in the maintenance labor and material cost that is a direct result of the predictive maintenance program. In most plants that we have evaluated over the past few years, both categories have shown marked, in too many cases orders of magnitude, increases in replacement parts, such as bearings, and wear parts. In one plant, the annual replacement cost for rolling-element bearings increased from $2.4 to $14.1 million dollars. Obviously, the labor cost required installing these added bearing also increased substantially. If the incremental cost has increased, it’s not working.
The second step is to evaluate the impact of predictive-driven maintenance tasks on the availability or production capacity of critical plant systems. In too many cases, these activities have increased the scheduled downtime needed for preventive or corrective maintenance. In effect, the predictive maintenance program has simply shifted unscheduled downtime to scheduled downtime. Since most plans consider scheduled downtime as a cost of doing business, this incremental lost capacity is not considered a negative.
Finally, evaluate the recommendations generated by the predictive program. If your vibration program is reporting bad bearings, misalignment, imbalance or mechanical looseness, it probably not providing real benefit. These are normally symptoms of underlying problems that must be corrected to prevent recurrence. Simply replacing bearings, or trying to correct misalignment, imbalance or looseness without correcting the reason that these abnormalities exist will only increase cost and reduce total capacity throughput. The same is true of thermography programs that only find loose connections, faulty fuses and other simple electrical problems or tribology problems that find dirty or contaminated lube oil. These kinds of results simply do not generate the reliability and life cycle cost improvements needed to justify the recurring cost of the program.
The effort required implementing and supporting an effective total plant predictive maintenance program is great, but so are the benefits that can be derived. Properly implemented and supported, predictive maintenance, as part of a life cycle asset management program, can reduce all the limiting factors, including breakdowns. At the same time, these programs will supply the asset reliability needed to increase throughput, incoming revenue and profitability.
Predictive maintenance can transform the maintenance operation from an expensive support function to a full member of the profit generating team in your plant. Do not expect an easy quick fix. Like all things of value, a certain amount of effort is needed to gain positive results. If you follow these steps, you can set up a total plant predictive maintenance program that will supply maximum benefits for your plant.
Shoreline AI, 1671 Dell Ave, Suite 208, Campbell, CA 95008
info@shorelineai.us
Copyright 2025 Shoreline AI All Rights Reserved.